摘 要:根據中國南海某氣田開發項目水下采油樹的應用環境及應用要求,對水下采油樹鋼結構焊接所產生的殘余應力的機理、分布規律及其影響因素進行了分析,闡述了控制水下采油樹鋼結構焊接殘余應力的主要工藝解決措施。在此基礎上,將其應用于國產化備用采油樹項目,結果證明其能滿足產品的應用要求。
中圖分類號:TE952 文獻標志碼:A 【DOI】10.13788/j.cnki.cbgc.2016.06.073
引言
水下采油樹作為海洋油氣開采中的水下生產系統的關鍵油氣生產控制設備,實際上就是位于海底井口頂端開口處的一個組件,它提供一系列用于原油生產、控制、測試及維修的通道和各種用來測量和維修的閥門。水下采油樹鋼結構的主要功能是為采油樹及零部件模塊提供水下安放支座及防護結構。水下采油樹鋼結構件長期沉浸于海底,遭受海水腐蝕,并接受陰極保護(犧牲陽極法),這種情況下鋼結構焊接后內部的殘余應力往往會誘發氫脆或氫致裂紋并加劇應力腐蝕。因此對于水下采油樹鋼結構的焊接,必須采取措施消減其焊后殘余應力。本文在對鋼結構焊接所產生的殘余應力的機理、分布規律及其影響因素進行分析的基礎上,提出了控制水下采油樹鋼結構焊接殘余應力的主要工藝解決措施。
1 水下采油樹鋼結構的應用要求及特點
1.1 水下采油樹鋼結構的工作環境
水下采油樹鋼結構主要包括樹框架(圖1)、永久導向基座(圖2)、樹整體取送工具(圖3)、防腐帽(圖4)、RPM 支架及ROV 操作面板等。水下采油樹鋼結構件長期浸于海底面臨海水腐蝕,并接受陰極保護[1]。
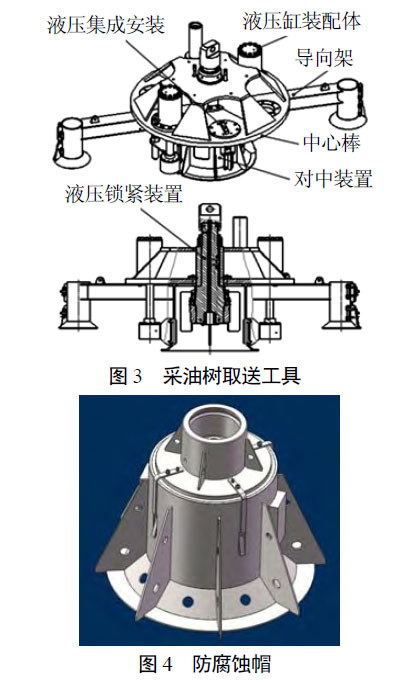
深海海底環境溫度較低,接近0℃。因此,水下采油樹鋼結構的材料應選用韌性及焊接性良好的低合金鋼,同時必須考慮焊接應力對陰極保護的敏感性及應力腐蝕傾向。
1.2 水下采油樹鋼結構焊接殘余應力的危害
水下采油樹鋼結構由于接受陰極保護(犧牲陽極法)[2],海水可作為電解質溶液,在構成電池反應時,作為陰極而接受保護的采油樹鋼結構的表面會發生析氫反應,生成的氫原子一部分會通過擴散進入金屬基體,在裂紋的尖端及應力集中處聚集,降低金屬晶格的內聚強度。由于氫與材料內部應力的共同作用會加劇開裂[3],水下采油樹鋼結構與其他水下設備一樣,其焊后殘余應力會誘發氫脆或氫致裂紋,并加劇應力腐蝕的敏感性。
對于水下采油樹鋼結構的焊接,盡管從材料設計及工藝參數選擇方面考慮都可降低焊接殘余應力及氫脆敏感性等,但焊接熱循環的作用使得殘余應力(拉應力)不可避免。因此,工藝上如何消除焊接殘余應力成為水下采油樹鋼結構工藝的關鍵。
2 鋼結構焊接殘余應力
2.1 焊接殘余應力概念
焊接應力是焊接構件因焊接熱循環而產生的應力。焊接過程的不均勻溫度場以及由其引起的局部塑性變形和比容不同的相組織是產生焊接應力的根本原因[4]。當焊接引起的不均勻溫度場尚未消失時,焊件中的這種應力和變形稱為瞬態焊接應力,焊接溫度場消失后的應力稱為焊接殘余應力。
2.2 焊接殘余應力對焊接鋼構件的影響
1)影響焊接構件剛度
由于內部焊接殘余應力的存在,當外部載荷還沒有達到材料的屈服極限時(實際上結構的外部載荷與內部應力之和已超過材料的屈服極限),就可能引起材料的屈服變形,喪失了進一步承受外部載荷的能力,這樣就相當于減小了材料的有效截面積,降低了剛度,對受壓桿件來說,也就降低了穩定性。
2)影響焊接構件靜載強度
一般來說,如不存在嚴重應力集中情況,只要材料具有允許的塑性變形能力,焊后殘余應力不會影響結構的靜載強度,但如果結構處于脆性狀態,殘余應力的存在則使結構承受外載的能力降低,導致結構過早破壞。
3)對焊接構件疲勞強度的影響
殘余應力的存在使變載荷的應力循環發生偏移,如應力集中處存在焊接殘余應力,將使疲勞強度降低。
4)加劇應力腐蝕開裂
應力腐蝕開裂是拉伸殘余應力和化學腐蝕共同作用下產生裂紋的現象,應力腐蝕開裂所需的時間與殘余應力大小有關,拉伸殘余應力越大,應力腐蝕開裂的時間越短。
5)影響加工精度及尺寸穩定性
當機械加工把一部分材料從焊件上切除時,此處的殘余應力也被釋放。殘余應力原來的平衡狀態被打破,這樣焊件會在加工的同時發生變形,導致加工精度受影響。
3 傳統的消除焊后殘余應力的工藝措施
在實際焊接過程中,可通過一定工藝措施來控制內部的應力,如調整工藝參數(焊接速度、焊接順序、接頭拘束度、焊接方向)、焊前預熱及反變形等。而對于焊后殘余應力的消除常采取以下措施。
3.1 利用高溫回火來消除焊接殘余應力
由于構件殘余應力的最大值通??蛇_到該種材料的屈服點,而金屬在高溫下的屈服點將降低,所以將構件的溫度升高至某一定數值時,應力的最大值也應該減少到該溫度下的屈服點數值。如果要完全消除結構中的殘余應力,則必須將構件加熱到其屈服點等于0 的溫度,所以一般所取的回火溫度接近于這個溫度。
1)整體高溫回火
將整個構件放在爐中加熱到一定溫度,然后保溫一段時間再冷卻。通過整體高溫回火可以將構件中80%~90%的殘余應力消除掉,這是生產中應用最廣泛、效果最好的一種消除殘余應力的方法?;鼗饡r間隨構件厚度而定,鋼按14 mm/h 計算,但不宜低于30min,但一般不高于3 h,因為殘余應力的消除效果隨時間迅速降低,所以過長的處理時間是不必要的。
2)局部高溫回火
只對焊縫及其局部區域進行加熱消除殘余應力。
消除應力的效果不如整體高溫回火,此方法設備簡單,常用于比較簡單的、剛度較小的構件,如長筒形容器、管道接頭、長構件的對接接頭等焊接殘余應力的消除。
3.2 利用溫差拉伸法來消除焊接殘余應力
溫差拉伸法消除焊接殘余應力的基本原理與機械拉伸法相同,主要差別是利用局部加熱的溫差來拉伸焊縫區。溫差拉伸法是在焊縫兩側各用一個寬度適當的氧乙炔焰焊炬進行加熱,在焊炬后面一定距離,用一根帶有排孔的水管進行噴水冷卻。氧乙炔焰和噴水管以相同速度向前移動。這就形成了一個兩側溫度高(峰值約為200 ℃)、焊接區溫度低(約為100 ℃)的溫度差。兩側金屬受熱膨脹對溫度較低的區域進行拉伸,這樣就可消除部分殘余應力。
3.3 利用振動法來消除焊接殘余應力
構件承受變載荷應力達到一定數值,經過多次循環加載后,結構中的殘余應力逐漸降低,即利用振動的方法可以消除部分焊接殘余應力。振動法的優點是設備簡單、成本低,時間比較短,沒有高溫回火時的氧化問題,已在生產上得到一定應用。
4 焊后殘余應力消除的工藝技術發展動態
4.1 傳統焊后殘余應力處理工藝的局限性
1)由于焊后熱處理會降低一部分的材料屬性,因此它不一定有益。尤其在較高的溫度條件中,有的材料的剛度會下降,且焊接熱影響區和熔融區因韌性變低而產生的裂紋,亦可以很大程度上改變其使用屬性。
利用熱處理也存在其他的約束條件,如退火爐的高額成本、復雜的配套工具和大量的能量使用等。
2)振動時效應用涉及有關多學科交叉領域,包括材料科學、熱力學和結構力學等,其原理也尚處于探索階段。在工藝處理方面仍然難以穩定可靠地改善金相結構和機械性能。由于振動時效具有不確定性,導致工程技術人員的經驗水平極大程度直接影響了工藝效果。
4.2 新型的焊后殘余應力處理工藝——
1)20 世紀70 年代,烏克蘭的Paton 研發中心第一個提出超聲波沖擊技術,并和俄羅斯的“量子”研發中心成功地聯合研發出此項技術,并首先投入到船舶焊接殘余應力領域。之后,( HPU )方面連續獲得突破,其應用涉及到多種材料、結構件和焊接單元方面。該技術至今在俄羅斯、烏克蘭、法國、日本、挪威、瑞典、加拿大和美國多個國家和地區的各個工程領域都有廣泛運用。
2)豪克能沖擊處理可以在焊接接頭表面形成壓縮塑性變形,產生壓應力,改善接頭殘余應力分布[6]。它通過高功率儀器產生20 000 次/秒左右的頻率沖擊物體金屬表層,高能量使得材料表面生成顯著的壓縮塑性變形,形成有利的壓縮應力和殘余應力場,同時,大能量沖擊使得材料表層溫度快速升高而后快速降低,可以使材料作用區表面晶粒組織細化,這樣就可以增加焊件的疲勞壽命,獲得抗應力腐蝕的能力。
3)隨著科技的發展,當今的UIT/UP 設備電源箱選用高質材料及元件,通過運用模塊設計,并采用最新的生產工藝制造,使得其控制電源具有頻率自動掃描、檢測、跟蹤和故障保護、功率調整、人機交流和程序升級等功能。豪克能沖擊焊接應力消除設備及應用如圖5 所示。
4)不同工藝殘余應力去除率的比較如表1 所示。
相關研究資料[5-7]表明,豪克能沖擊技術能夠大幅度消除鋼制焊接接頭殘余應力,并改善疲勞強度。
5)豪克能沖擊技術是目前所有消除焊接殘余應力的工藝手段中最徹底、最有效的消除方式。
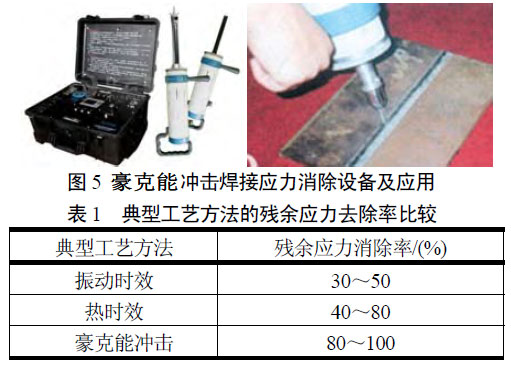
圖5 沖擊焊接應力消除設備及應用
表1 典型工藝方法的殘余應力去除率比較
典型工藝方法 殘余應力消除率/(%)
振動時效 30~50
熱時效 40~80
豪克能沖擊 80~100
5 水下采油樹中鋼結構焊接殘后殘余應力消除工藝
因水下采油樹焊接構件整體尺寸比較大,如采用傳統的熱處理退火工藝消除焊接殘余應力,要求爐體尺寸大,不僅成本高昂,而且效率低?;谝陨系募夹g分析,在中國南海某油氣開采項目中,為增強鋼結構抵抗氫致裂紋及應力腐蝕的能力,國產化備用水下采油樹鋼結構的焊后應力消除采取振動時效+超聲波沖擊的組合工藝。
1)振動時效:其主要作用是對構件整體的殘余應力降低并均化。
2)豪克能沖擊:其作用是消除焊縫接頭區的有害拉應力,細化接頭區金屬晶粒組織。
6 結論
1)水下采油樹鋼結構的焊接須考慮陰極保護效應導致的氫致裂紋及應力腐蝕傾向。
2)接受陰極保護(犧牲陽極法)的水下采油樹鋼結構的焊后殘余應力會誘發氫脆或氫致裂紋,并加劇應力腐蝕。工藝上如何消除焊接殘余應力成為水下采油樹鋼結構工藝的關鍵。
3)傳統焊后殘余應力處理措施(如焊后退火、振動時效等)存在一定的局限性。豪克能超聲沖擊技術是目前所有消除焊接殘余應力的工藝手段中消除率最大化、z有效的消除方式。
4)水下采油樹鋼結構焊后采取振動時效+豪克能沖擊的組合工藝進行消除應力處理,有利于增強鋼結構抵抗氫致裂紋及應力腐蝕的能力。